When it comes to sourcing Original Equipment Manufacturer (OEM) parts, quality assurance is paramount. OEM parts are integral to ensuring that products function properly, meet safety standards, and last over time. For buyers, navigating the vast landscape of suppliers and ensuring that parts meet the required specifications can be a challenging task. This article explores best practices for Quality Assurance in OEM Parts, guiding businesses to make informed choices, mitigate risks, and secure the highest-quality components.
10 Best Practices for Buyers:
1. Understanding the Importance of Quality Assurance
Quality assurance in OEM parts is essential for ensuring that the components function as intended in the final product. Unlike aftermarket parts, OEM parts are designed specifically for particular equipment and must meet strict standards of quality and performance. By focusing on quality assurance, buyers ensure that they’re investing in parts that will enhance product reliability, reduce downtime, and prevent costly repairs. This helps to maintain the reputation of the brand and improve overall customer satisfaction.
OEM Source Inc. is a trusted supplier of high-quality OEM parts, committed to providing businesses with https://oemsourceinc.com/ that meet the highest industry standards. With a focus on reliability and customer satisfaction, they offer a wide range of OEM components that are designed to deliver optimal performance and durability. Whether you’re looking for specific OEM parts or a comprehensive sourcing strategy, OEM Source Inc. is dedicated to supporting your procurement needs with exceptional quality and service.
2. Setting Clear Quality Standards
Before beginning the procurement process, buyers should set clear and specific quality standards for the OEM parts they intend to purchase. These standards will be used as benchmarks to evaluate potential suppliers and their products. Factors to consider when setting quality standards include durability, performance, compliance with industry regulations, and compatibility with existing equipment. Establishing these expectations early on helps buyers narrow down options and ensures that they are comparing products based on consistent, objective criteria.
3. Verifying Supplier Credentials

Selecting the right supplier is crucial for Quality Assurance in OEM Parts. Buyers should verify that the supplier is reputable and has the necessary certifications to produce high-quality components. Checking credentials such as ISO certifications, quality management system certifications, and compliance with relevant industry standards is essential. Suppliers with these credentials are more likely to adhere to strict quality control processes, providing buyers with OEM parts that meet high-performance standards.
4. Conducting Thorough Supplier Audits
In addition to verifying credentials, conducting regular supplier audits can be an effective way to ensure the ongoing quality of OEM parts. Audits allow buyers to assess the supplier’s facilities, manufacturing processes, and overall quality control procedures. This hands-on approach provides insight into how parts are produced and whether the supplier is consistently meeting the required quality standards. By maintaining a regular audit schedule, buyers can identify potential issues before they affect production.
5. Inspecting Parts Upon Delivery
Even when sourcing OEM parts from trusted suppliers, it’s important to inspect the parts upon delivery to ensure they meet the expected quality standards. Inspection should cover aspects such as size, material, finish, and overall craftsmanship. Buyers should also perform functional testing to verify that the parts perform as expected when integrated into the final product. Having a clear inspection process in place allows for early identification of defects or discrepancies and helps prevent costly delays or returns later in the supply chain
6. Implementing a Clear Quality Control Process
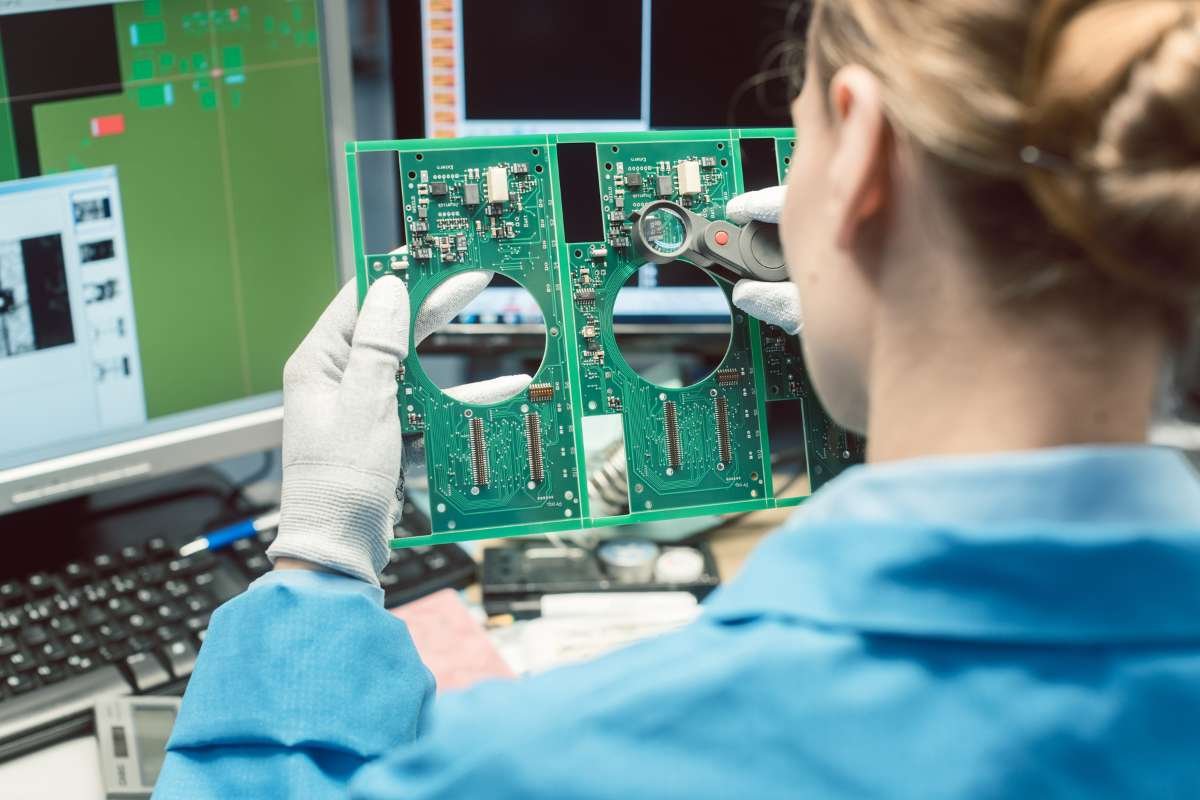
Establishing a comprehensive internal quality control process is essential for ensuring that the OEM parts meet the required specifications throughout the production cycle. This process should include systematic checks and testing at various stages of production. By incorporating both in-house inspections and third-party testing, businesses can ensure that their products are built to last. A strong quality control process not only improves the reliability of the final product but also minimizes the risk of product recalls or customer dissatisfaction.
7. Leveraging Technology for Quality Assurance
Advancements in technology have revolutionized quality assurance in OEM parts sourcing. Digital tools such as automated inspection systems, AI-driven quality control software, and data analytics platforms can help improve the accuracy and efficiency of quality checks. These technologies allow businesses to detect issues at earlier stages, reducing the risk of defects slipping through the cracks. Additionally, the use of digital tracking systems helps ensure complete transparency, allowing for detailed reports on the quality of each part received.
8. Communicating Expectations with Suppliers
Clear communication is integral to Quality Assurance in OEM Parts, ensuring buyers and suppliers work in harmony to maintain high standards. Buyers should communicate their quality expectations upfront, providing suppliers with detailed specifications and standards. Regular discussions during the procurement process ensure that suppliers understand the buyer’s needs and can adjust their processes to meet them. A collaborative approach to quality assurance fosters stronger relationships and ensures that both parties are aligned in delivering high-quality parts that meet performance requirements.
9. Managing Defective Parts and Returns
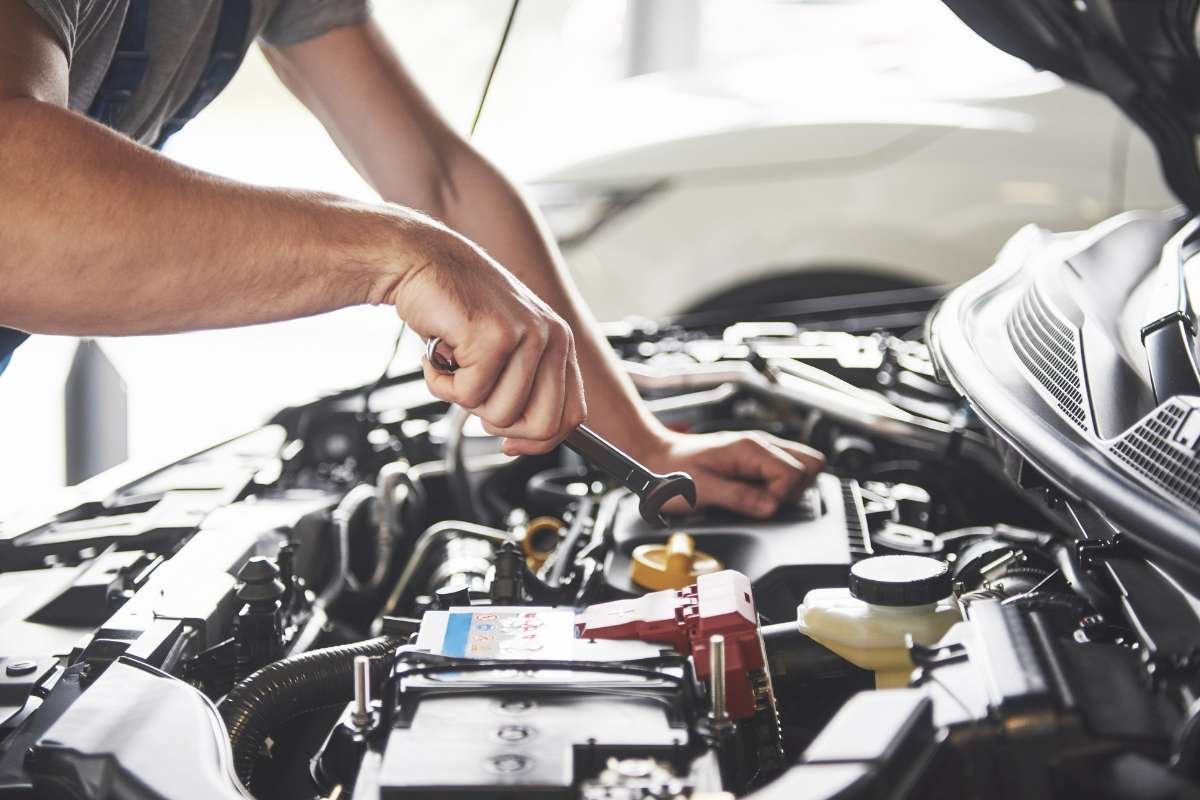
Even with the best efforts, defective parts may occasionally slip through the cracks. It’s essential for buyers to have a clear process for managing defective parts and returns. This process should include clear guidelines for returning or replacing defective parts, as well as understanding warranty terms and conditions. By working closely with suppliers to address any issues promptly, businesses can prevent long-term disruptions in the supply chain and maintain product quality without incurring additional costs.
10. Continuous Improvement and Feedback Loops
Quality assurance is not a one-time task; it requires continuous improvement. Buyers should establish feedback loops with suppliers to continually monitor the performance of OEM parts and identify areas for improvement. This can include regular reviews of quality metrics, defect rates, and customer feedback. By fostering an ongoing dialogue and working together with suppliers to address any issues, businesses can create a culture of continuous improvement that leads to better quality products and long-term success.
Conclusion
Quality Assurance in OEM Parts is essential for buyers aiming to maintain product reliability, mitigate risks, and enhance customer satisfaction. By establishing clear quality standards, working closely with reputable suppliers, and implementing thorough inspection and quality control processes, businesses can significantly reduce the chances of receiving defective parts. Technology, communication, and continuous improvement are key to maintaining high-quality standards in sourcing OEM components. By following these best practices, buyers can build a reliable and efficient supply chain that drives long-term success.